Технология резки пластин, являющаяся важнейшим этапом в процессе производства полупроводников, напрямую связана с производительностью микросхем, выходом годных изделий и себестоимостью производства.
#01 Предыстория и значение нарезки пластин
1.1 Определение нарезки вафель
Нарезка пластин (также известная как скрайбирование) является важным этапом в производстве полупроводников, направленным на разделение обработанных пластин на несколько отдельных кристаллов. Эти кристаллы обычно содержат полную функциональность схемы и являются основными компонентами, в конечном итоге используемыми в производстве электронных устройств. Поскольку конструкции чипов становятся все более сложными, а размеры продолжают уменьшаться, требования к точности и эффективности технологии нарезки пластин становятся все более строгими.
В практических операциях для резки пластин обычно используются высокоточные инструменты, такие как алмазные лезвия, чтобы гарантировать, что каждая матрица остается целой и полностью функциональной. Ключевые этапы включают подготовку перед резкой, точный контроль во время процесса резки и проверку качества после резки.
Перед резкой пластина должна быть размечена и позиционирована для обеспечения точных траекторий резки. Во время резки такие параметры, как давление инструмента и скорость, должны строго контролироваться, чтобы не повредить пластину. После резки проводятся комплексные проверки качества, чтобы гарантировать, что каждый чип соответствует стандартам производительности.
Фундаментальные принципы технологии резки пластин охватывают не только выбор режущего оборудования и настройку параметров процесса, но и влияние механических свойств и характеристик материалов на качество резки. Например, низко-k диэлектрические кремниевые пластины из-за своих худших механических свойств сильно подвержены концентрации напряжений во время резки, что приводит к таким отказам, как сколы и трещины. Низкая твердость и хрупкость низко-k материалов делают их более подверженными структурным повреждениям под действием механической силы или термического напряжения, особенно во время резки. Контакт между инструментом и поверхностью пластины в сочетании с высокими температурами может еще больше усугубить концентрацию напряжений.
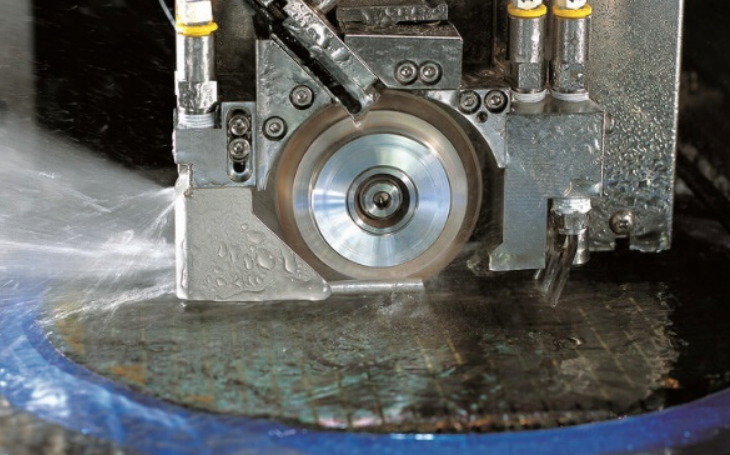
С развитием материаловедения технология резки пластин вышла за рамки традиционных полупроводников на основе кремния и включила новые материалы, такие как нитрид галлия (GaN). Эти новые материалы, благодаря своей твердости и структурным свойствам, создают новые проблемы для процессов резки, требуя дальнейшего совершенствования инструментов и методов резки.
Как важнейший процесс в полупроводниковой промышленности, резка пластин продолжает совершенствоваться в ответ на растущие требования и технологические достижения, закладывая основу для будущих технологий микроэлектроники и интегральных схем.
Улучшения в технологии резки пластин выходят за рамки разработки вспомогательных материалов и инструментов. Они также включают оптимизацию процесса, повышение производительности оборудования и точный контроль параметров резки. Эти усовершенствования направлены на обеспечение высокой точности, эффективности и стабильности в процессе резки пластин, удовлетворяя потребности полупроводниковой промышленности в меньших размерах, более высокой интеграции и более сложных структурах чипов.
Зона улучшения | Конкретные меры | Эффекты |
Оптимизация процесса | - Улучшение первоначальной подготовки, например, более точное позиционирование пластин и планирование пути. | - Уменьшение ошибок резки и повышение стабильности. |
- Минимизация ошибок резки и повышение стабильности. | - Внедрение механизмов мониторинга и обратной связи в реальном времени для регулировки давления, скорости и температуры инструмента. | |
- Снижение частоты поломок пластин и улучшение качества чипов. | ||
Повышение производительности оборудования | - Использование высокоточных механических систем и передовых технологий автоматизации управления. | - Повышение точности резки и сокращение отходов материала. |
- Внедрить технологию лазерной резки, пригодную для пластин из материалов высокой твердости. | - Повышение эффективности производства и сокращение ручных ошибок. | |
- Повышение автоматизации оборудования для автоматического контроля и регулировки. | ||
Точный контроль параметров | - Тонкая настройка таких параметров, как глубина резания, скорость, тип инструмента и методы охлаждения. | - Обеспечение целостности кристалла и электрических характеристик. |
- Настройте параметры на основе материала, толщины и структуры пластины. | - Повышение производительности, сокращение отходов материалов и снижение производственных затрат. | |
Стратегическое значение | - Постоянно изучать новые технологические пути, оптимизировать процессы и расширять возможности оборудования для удовлетворения потребностей рынка. | - Повышение производительности и выхода годных микросхем за счет поддержки разработки новых материалов и усовершенствованных конструкций микросхем. |
1.2 Важность нарезки пластин
Нарезка пластин играет важную роль в процессе производства полупроводников, напрямую влияя на последующие этапы, а также на качество и производительность конечного продукта. Ее важность можно описать следующим образом:
Во-первых, точность и последовательность резки являются ключевыми для обеспечения выхода годных чипов и надежности. В процессе производства пластины проходят несколько этапов обработки для формирования многочисленных сложных структур схем, которые должны быть точно разделены на отдельные чипы (кристаллы). Если в процессе резки есть существенные ошибки в выравнивании или резке, схемы могут быть повреждены, что повлияет на функциональность и надежность чипа. Таким образом, технология высокоточной резки не только обеспечивает целостность каждого чипа, но и предотвращает повреждение внутренних схем, улучшая общую норму выхода годных.
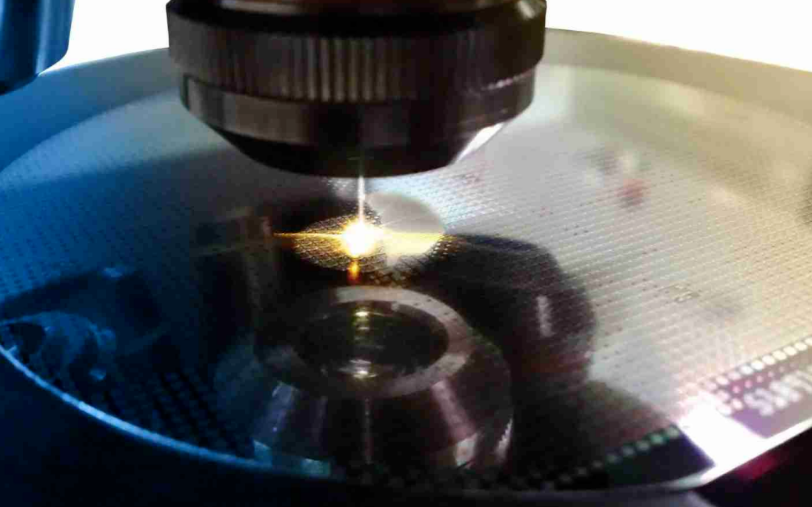
Во-вторых, нарезка пластин оказывает значительное влияние на эффективность производства и контроль затрат. Как важный этап в производственном процессе, ее эффективность напрямую влияет на ход последующих этапов. Оптимизируя процесс нарезки, повышая уровень автоматизации и улучшая скорость резки, можно значительно повысить общую эффективность производства.
С другой стороны, отходы материала во время резки являются критическим фактором в управлении затратами. Использование передовых технологий резки не только сокращает ненужные потери материала во время процесса резки, но и повышает коэффициент использования пластин, тем самым снижая производственные затраты.
С развитием полупроводниковых технологий диаметры пластин продолжают увеличиваться, а плотность схем соответственно повышается, что предъявляет более высокие требования к технологии резки. Более крупные пластины требуют более точного контроля траекторий резки, особенно в областях с высокой плотностью схем, где даже незначительные отклонения могут привести к дефектам нескольких чипов. Кроме того, более крупные пластины требуют большего количества линий резки и более сложных этапов процесса, что требует дальнейшего улучшения точности, согласованности и эффективности технологий резки для решения этих задач.
1.3 Процесс нарезки пластин
Процесс резки пластин охватывает все этапы от фазы подготовки до окончательной проверки качества, причем каждый этап имеет решающее значение для обеспечения качества и производительности нарезанных пластин. Ниже приводится подробное объяснение каждой фазы.
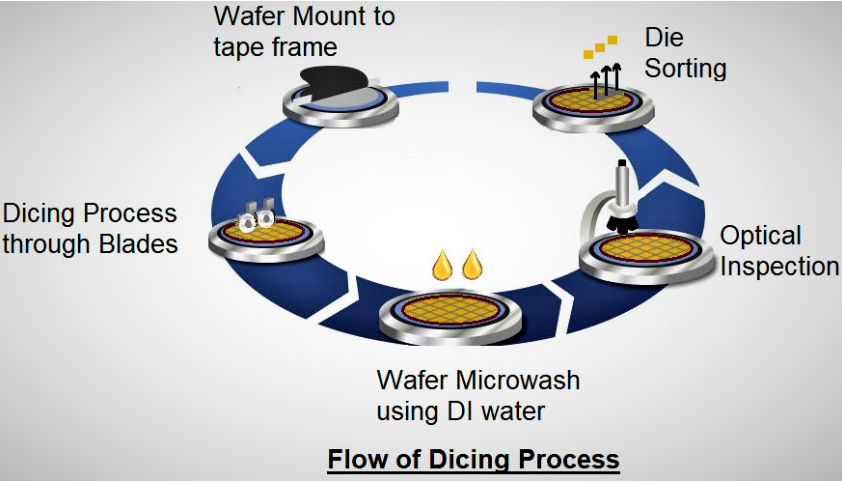
Фаза | Подробное описание |
Подготовительная фаза | -Очистка пластин: Используйте чистую воду и специальные чистящие средства в сочетании с ультразвуковой или механической очисткой для удаления загрязнений, частиц и пыли, обеспечивая чистую поверхность. -Точное позиционирование: Используйте высокоточное оборудование, чтобы гарантировать точное разделение пластины по заданным траекториям резки. -Фиксация пластины: Закрепите пластину на рамке из ленты, чтобы сохранить устойчивость во время резки, предотвращая повреждения из-за вибрации или движения. |
Фаза резки | -Нарезка кубиками лезвий: Используйте высокоскоростные вращающиеся лезвия с алмазным покрытием для физической резки, подходящие для материалов на основе кремния и экономичные. -Лазерная нарезка кубиками: использование высокоэнергетических лазерных лучей для бесконтактной резки, идеально подходящей для хрупких или высокотвердых материалов, таких как нитрид галлия, обеспечивающей более высокую точность и меньшие потери материала. -Новые Технологии: Внедрение технологий лазерной и плазменной резки для дальнейшего повышения эффективности и точности при минимизации зон термического воздействия. |
Фаза очистки | - Используйте деионизированную воду (ДИ) и специальные чистящие средства в сочетании с ультразвуковой или распылительной очисткой для удаления мусора и пыли, образующихся в процессе резки, предотвращая влияние остатков на последующие процессы или электрические характеристики стружки. - Высокоочищенная деионизированная вода предотвращает попадание новых загрязняющих веществ, обеспечивая чистую среду пластин. |
Фаза инспекции | -Оптический осмотр: Используйте оптические системы обнаружения в сочетании с алгоритмами искусственного интеллекта для быстрого выявления дефектов, гарантируя отсутствие трещин и сколов на нарезанных чипсах, повышая эффективность контроля и сокращая количество человеческих ошибок. -Измерение размеров: Убедитесь, что размеры чипа соответствуют проектным спецификациям. -Испытание электрических характеристик: Обеспечение соответствия электрических характеристик критически важных микросхем стандартам, гарантирующее надежность в последующих приложениях. |
Фаза сортировки | - Используйте роботизированные руки или вакуумные присоски для отделения годных чипов от ленточной рамки и автоматической сортировки их по производительности, обеспечивая эффективность и гибкость производства, а также повышая точность. |
Процесс резки пластин включает в себя очистку пластин, позиционирование, резку, очистку, проверку и сортировку, причем каждый шаг имеет решающее значение. Благодаря достижениям в области автоматизации, лазерной резки и технологий проверки с использованием искусственного интеллекта современные системы резки пластин могут достигать более высокой точности, скорости и меньших потерь материала. В будущем новые технологии резки, такие как лазерная и плазменная, постепенно заменят традиционную резку лезвиями, чтобы удовлетворить потребности все более сложных конструкций чипов, что еще больше стимулирует развитие процессов производства полупроводников.
Технология резки пластин и ее принципы
На рисунке показаны три распространённые технологии резки пластин:Нарезка кубиками лезвий,Лазерная нарезка кубиками, иПлазменная резка. Ниже приведен подробный анализ и дополнительное объяснение этих трех методов:
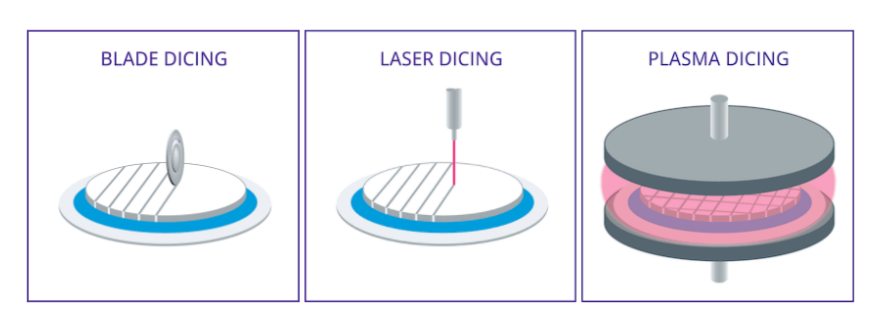
В производстве полупроводников резка пластин является важным этапом, который требует выбора соответствующего метода резки в зависимости от толщины пластины. Первым шагом является определение толщины пластины. Если толщина пластины превышает 100 микрон, в качестве метода резки можно выбрать метод лезвийной резки. Если лезвийная резка не подходит, можно использовать метод дробления, который включает в себя как методы резки скрайбированием, так и методы лезвийной резки.
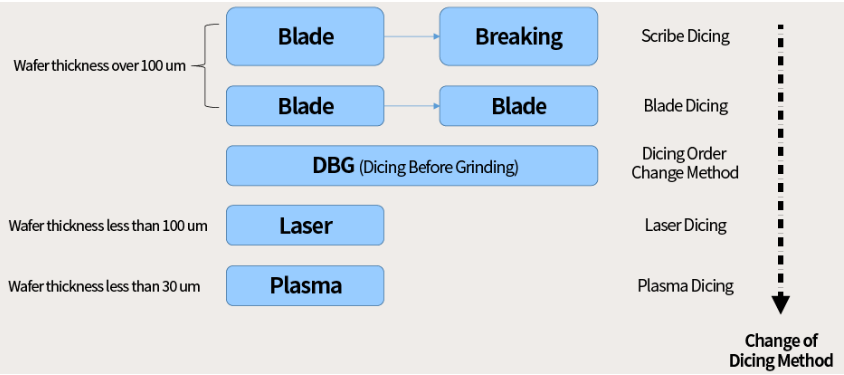
Если толщина пластины составляет от 30 до 100 микрон, рекомендуется метод DBG (Dice Before Grinding). В этом случае можно выбрать резку скрайбом, резку лезвием или корректировку последовательности резки по мере необходимости для достижения наилучших результатов.
Для сверхтонких пластин толщиной менее 30 микрон лазерная резка становится предпочтительным методом из-за ее способности точно резать тонкие пластины, не вызывая чрезмерных повреждений. Если лазерная резка не может удовлетворить определенным требованиям, плазменная резка может быть использована в качестве альтернативы. Эта блок-схема обеспечивает четкий путь принятия решений, чтобы гарантировать, что выбрана наиболее подходящая технология резки пластин в условиях различной толщины.
2.1 Технология механической резки
Технология механической резки является традиционным методом резки пластин. Основной принцип заключается в использовании высокоскоростного вращающегося алмазного шлифовального круга в качестве режущего инструмента для нарезки пластины. Ключевое оборудование включает в себя шпиндель на воздушном подшипнике, который приводит в движение алмазный шлифовальный круг на высоких скоростях для выполнения точной резки или проточки канавок по заданной траектории резки. Эта технология широко используется в промышленности из-за ее низкой стоимости, высокой эффективности и широкой применимости.
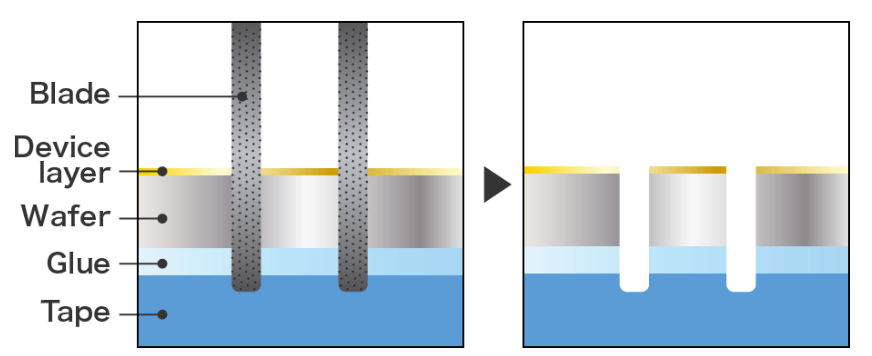
Преимущества
Высокая твердость и износостойкость алмазных шлифовальных кругов позволяет технологии механической резки адаптироваться к потребностям резки различных материалов пластин, будь то традиционные материалы на основе кремния или новые полупроводниковые соединения. Его работа проста, с относительно низкими техническими требованиями, что еще больше способствует его популярности в массовом производстве. Кроме того, по сравнению с другими методами резки, такими как лазерная резка, механическая резка имеет более контролируемые затраты, что делает ее подходящей для нужд крупносерийного производства.
Ограничения
Несмотря на многочисленные преимущества, технология механической резки также имеет ограничения. Во-первых, из-за физического контакта между инструментом и пластиной точность резки относительно ограничена, что часто приводит к отклонениям размеров, которые могут повлиять на точность последующей упаковки и тестирования чипов. Во-вторых, в процессе механической резки могут легко возникнуть такие дефекты, как сколы и трещины, что не только влияет на выход годного, но и может негативно сказаться на надежности и сроке службы чипов. Повреждения, вызванные механическим напряжением, особенно пагубны для производства чипов высокой плотности, особенно при резке хрупких материалов, где эти проблемы более заметны.
Технологические усовершенствования
Чтобы преодолеть эти ограничения, исследователи постоянно оптимизируют процесс механической резки. Ключевые усовершенствования включают улучшение конструкции и выбор материала шлифовальных кругов для повышения точности и долговечности резки. Кроме того, оптимизация структурной конструкции и систем управления режущим оборудованием еще больше повысила стабильность и автоматизацию процесса резки. Эти достижения уменьшают количество ошибок, вызванных человеческими операциями, и улучшают последовательность резки. Внедрение передовых технологий инспекции и контроля качества для мониторинга аномалий в реальном времени во время процесса резки также значительно повысило надежность и производительность резки.
Будущее развитие и новые технологии
Хотя технология механической резки по-прежнему занимает важное место в резке пластин, новые технологии резки быстро развиваются по мере развития полупроводниковых процессов. Например, применение технологии термической лазерной резки обеспечивает новые решения проблем точности и дефектов при механической резке. Этот бесконтактный метод резки снижает физическую нагрузку на пластину, значительно снижая частоту сколов и трещин, особенно при резке более хрупких материалов. В будущем интеграция технологии механической резки с новыми методами резки предоставит производству полупроводников больше возможностей и гибкости, что еще больше повысит эффективность производства и качество чипов.
В заключение следует отметить, что, хотя технология механической резки имеет определенные недостатки, постоянное совершенствование технологий и ее интеграция с новыми методами резки позволяют ей по-прежнему играть важную роль в производстве полупроводников и сохранять свою конкурентоспособность в будущих процессах.
2.2 Технология лазерной резки
Технология лазерной резки, как новый метод резки пластин, постепенно завоевала широкое внимание в полупроводниковой промышленности благодаря своей высокой точности, отсутствию механических контактных повреждений и быстрой резке. Эта технология использует высокую плотность энергии и фокусирующую способность лазерного луча для создания небольшой зоны термического воздействия на поверхности материала пластины. Когда лазерный луч воздействует на пластину, создаваемое термическое напряжение вызывает разрушение материала в указанном месте, достигая точной резки.
Преимущества технологии лазерной резки
• Высокая точность: Возможность точного позиционирования лазерного луча позволяет достигать точности резки на уровне микронов и даже нанометров, что соответствует требованиям современного высокоточного производства интегральных схем высокой плотности.
• Отсутствие механического контакта: Лазерная резка исключает физический контакт с пластиной, предотвращая распространенные проблемы при механической резке, такие как сколы и трещины, что значительно повышает выход годных изделий и надежность чипов.
• Высокая скорость резки: Высокая скорость лазерной резки способствует повышению эффективности производства, что делает ее особенно подходящей для крупномасштабных высокоскоростных производственных сценариев.
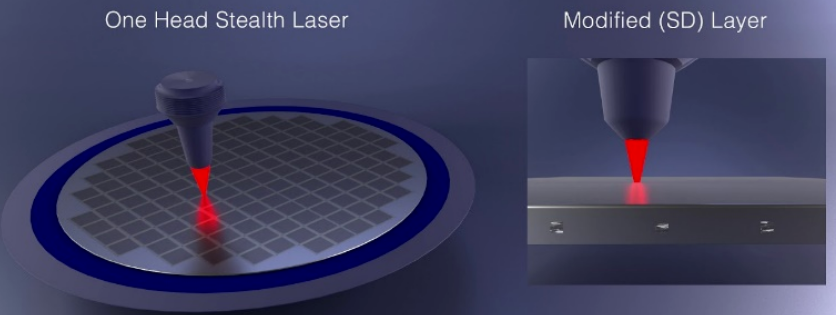
Проблемы, с которыми пришлось столкнуться
• Высокая стоимость оборудования: Первоначальные инвестиции в оборудование для лазерной резки высоки, что создает экономическое давление, особенно для малых и средних производственных предприятий.
• Комплексное управление процессами: Лазерная резка требует точного контроля нескольких параметров, включая плотность энергии, положение фокуса и скорость резки, что усложняет процесс.
• Проблемы с зоной теплового воздействия: Хотя бесконтактная природа лазерной резки снижает механические повреждения, термическое напряжение, вызванное зоной термического влияния (ЗТВ), может негативно влиять на свойства материала пластины. Для минимизации этого эффекта необходима дальнейшая оптимизация процесса.
Направления технологического совершенствования
Для решения этих проблем исследователи сосредотачиваются на снижении затрат на оборудование, повышении эффективности резки и оптимизации технологического процесса.
• Эффективные лазеры и оптические системы: Разрабатывая более эффективные лазеры и усовершенствованные оптические системы, можно снизить затраты на оборудование, одновременно повысив точность и скорость резки.
• Оптимизация параметров процесса: Проводятся углубленные исследования взаимодействия лазеров и материалов пластин с целью усовершенствования процессов, которые уменьшают зону термического влияния, тем самым повышая качество резки.
• Интеллектуальные системы управления: Развитие интеллектуальных технологий управления направлено на автоматизацию и оптимизацию процесса лазерной резки, повышение его стабильности и последовательности.
Технология лазерной резки особенно эффективна в сверхтонких пластинах и сценариях высокоточной резки. По мере увеличения размеров пластин и плотности схем традиционные методы механической резки не могут удовлетворить требованиям высокой точности и эффективности современного производства полупроводников. Благодаря своим уникальным преимуществам лазерная резка становится предпочтительным решением в этих областях.
Хотя технология лазерной резки по-прежнему сталкивается с такими проблемами, как высокая стоимость оборудования и сложность процесса, ее уникальные преимущества в высокой точности и бесконтактном повреждении делают ее важным направлением развития в производстве полупроводников. Поскольку лазерные технологии и интеллектуальные системы управления продолжают совершенствоваться, ожидается, что лазерная резка еще больше повысит эффективность и качество резки пластин, что будет способствовать непрерывному развитию полупроводниковой промышленности.
2.3 Технология плазменной резки
Технология плазменной резки, как новый метод резки пластин, привлекла значительное внимание в последние годы. Эта технология использует высокоэнергетические плазменные лучи для точной резки пластин, контролируя энергию, скорость и траекторию резки плазменного луча, достигая оптимальных результатов резки.
Принцип работы и преимущества
Процесс плазменной резки основан на высокотемпературном, высокоэнергетическом плазменном луче, генерируемом оборудованием. Этот луч может нагревать материал пластины до точки плавления или испарения за очень короткое время, что обеспечивает быструю резку. По сравнению с традиционной механической или лазерной резкой плазменная резка быстрее и создает меньшую зону термического воздействия, эффективно снижая возникновение трещин и повреждений во время резки.
В практическом применении технология плазменной резки особенно искусна в обработке пластин сложной формы. Ее высокоэнергетический, регулируемый плазменный луч может легко резать пластины неправильной формы с высокой точностью. Поэтому в производстве микроэлектроники, особенно в индивидуальном и мелкосерийном производстве высококачественных чипов, эта технология показывает большие перспективы для широкого использования.
Проблемы и ограничения
Несмотря на многочисленные преимущества технологии плазменной резки, она также сталкивается с некоторыми проблемами.
• Сложный процесс: Процесс плазменной резки сложен и требует высокоточного оборудования и опытных операторов для обеспеченияточность и стабильность резки.
• Экологический контроль и безопасность: Высокотемпературная и высокоэнергетическая природа плазменного пучка требует строгого контроля окружающей среды и мер безопасности, что увеличивает сложность и стоимость внедрения.
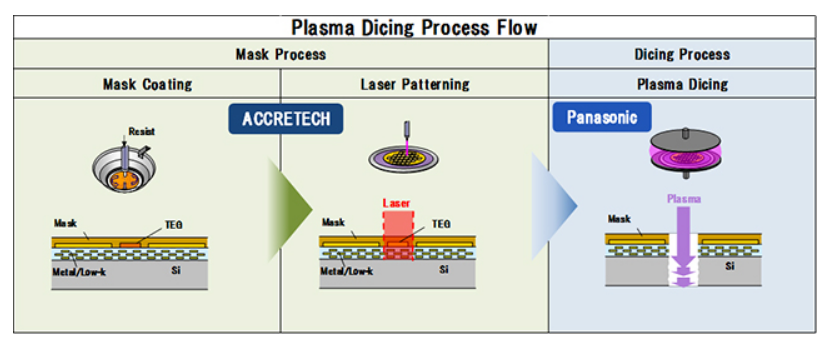
Будущие направления развития
Ожидается, что с развитием технологий проблемы, связанные с плазменной резкой, будут постепенно преодолены. Разрабатывая более интеллектуальное и стабильное режущее оборудование, можно снизить зависимость от ручных операций, тем самым повысив эффективность производства. В то же время оптимизация параметров процесса и среды резки поможет снизить риски безопасности и эксплуатационные расходы.
В полупроводниковой промышленности инновации в технологии резки и нарезки пластин имеют решающее значение для развития отрасли. Технология плазменной резки с ее высокой точностью, эффективностью и способностью обрабатывать сложные формы пластин стала важным новым игроком в этой области. Хотя некоторые проблемы остаются, они будут постепенно решаться с помощью постоянных технологических инноваций, что принесет больше возможностей и перспектив в производство полупроводников.
Перспективы применения технологии плазменной резки огромны, и ожидается, что в будущем она будет играть более важную роль в производстве полупроводников. Благодаря постоянным технологическим инновациям и оптимизации плазменная резка не только решит существующие проблемы, но и станет мощным драйвером роста полупроводниковой промышленности.
2.4 Качество резки и факторы, влияющие на него
Качество резки пластин имеет решающее значение для последующей упаковки чипов, тестирования и общей производительности и надежности конечного продукта. Распространенные проблемы, возникающие во время резки, включают трещины, сколы и отклонения резки. На эти проблемы влияют несколько факторов, работающих вместе.
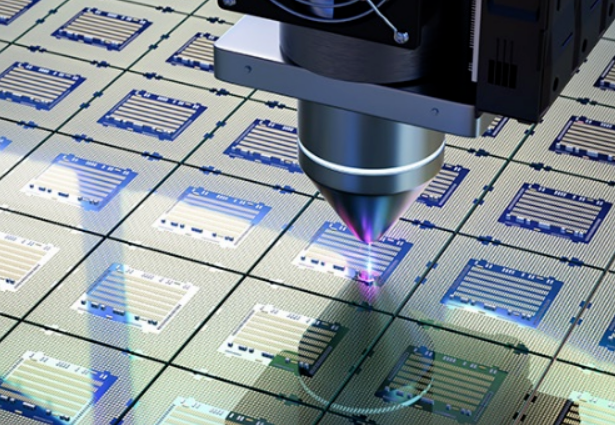
Категория | Содержание | Влияние |
Параметры процесса | Скорость резки, скорость подачи и глубина резки напрямую влияют на стабильность и точность процесса резки. Неправильные настройки могут привести к концентрации напряжений и чрезмерной зоне термического влияния, что приводит к трещинам и сколам. Правильная настройка параметров на основе материала пластины, толщины и требований к резке является ключом к достижению желаемых результатов резки. | Правильные параметры процесса обеспечивают точную резку и снижают риск возникновения дефектов, таких как трещины и сколы. |
Факторы оборудования и материалов | -Качество лезвия: Материал, твердость и износостойкость лезвия влияют на плавность процесса резки и плоскостность поверхности реза. Лезвия низкого качества увеличивают трение и термическое напряжение, что может привести к трещинам или сколам. Выбор правильного материала лезвия имеет решающее значение. -Эффективность охлаждающей жидкости: Охлаждающие жидкости помогают снизить температуру резки, минимизировать трение и очистить от мусора. Неэффективная охлаждающая жидкость может привести к высоким температурам и накоплению мусора, что влияет на качество и эффективность резки. Выбор эффективных и экологически чистых охлаждающих жидкостей имеет жизненно важное значение. | Качество лезвия влияет на точность и гладкость реза. Неэффективная охлаждающая жидкость может привести к плохому качеству и эффективности резки, что подчеркивает необходимость оптимального использования охлаждающей жидкости. |
Контроль процесса и проверка качества | -Управление процессами: Мониторинг и регулировка ключевых параметров резки в режиме реального времени для обеспечения стабильности и последовательности процесса резки. -Проверка качества: Проверка внешнего вида после резки, измерения размеров и испытания электрических характеристик помогают оперативно выявлять и устранять проблемы качества, повышая точность и однородность резки. | Правильный контроль процесса и контроль качества помогают обеспечить стабильные, высококачественные результаты резки и раннее выявление потенциальных проблем. |

Улучшение качества резки
Улучшение качества резки требует комплексного подхода, который учитывает параметры процесса, выбор оборудования и материалов, контроль процесса и инспекцию. Постоянно совершенствуя технологии резки и оптимизируя методы процесса, можно еще больше повысить точность и стабильность резки пластин, обеспечивая более надежную техническую поддержку для полупроводниковой промышленности.
#03 Обработка и тестирование после резки
3.1 Очистка и сушка
Этапы очистки и сушки после резки пластин имеют решающее значение для обеспечения качества чипа и плавного хода последующих процессов. На этом этапе важно тщательно удалить остатки кремния, остатки охлаждающей жидкости и другие загрязнения, образующиеся во время резки. Не менее важно убедиться, что чипы не повреждены в процессе очистки, а после сушки убедиться, что на поверхности чипа не осталось влаги, чтобы предотвратить такие проблемы, как коррозия или электростатический разряд.
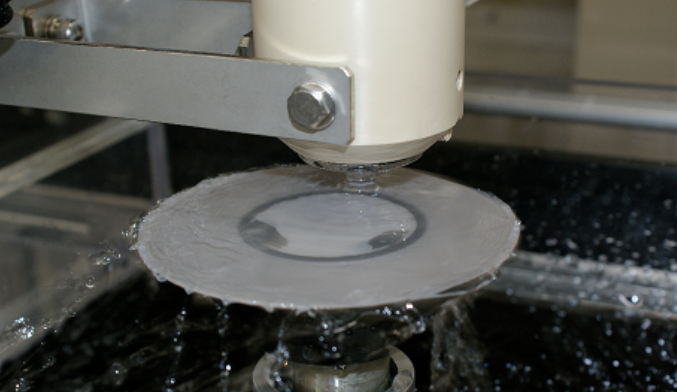
Обработка после резки: процесс очистки и сушки
Шаг процесса | Содержание | Влияние |
Процесс очистки | -Метод: Для очистки используйте специальные чистящие средства и чистую воду в сочетании с ультразвуковой или механической очисткой. | Обеспечивает тщательное удаление загрязнений и предотвращает повреждение стружки во время очистки. |
-Выбор чистящего средства: Выбирайте на основе материала пластины и типа загрязняющих веществ, чтобы обеспечить эффективную очистку без повреждения чипа. | Правильный выбор средства имеет решающее значение для эффективной очистки и защиты от сколов. | |
-Контроль параметров: Строго контролируйте температуру, время и концентрацию чистящего раствора во избежание проблем с качеством, вызванных неправильной очисткой. | Контроль помогает избежать повреждения пластины или появления загрязнений, обеспечивая стабильное качество. | |
Процесс сушки | -Традиционные методы: Естественная сушка воздухом и сушка горячим воздухом имеют низкую эффективность и могут привести к накоплению статического электричества. | Может привести к более медленному высыханию и потенциальным проблемам со статическим электричеством. |
-Современные Технологии: Используйте передовые технологии, такие как вакуумная сушка и инфракрасная сушка, чтобы гарантировать быстрое высыхание чипсов и избежать вредного воздействия. | Более быстрый и эффективный процесс сушки, снижающий риск возникновения статического разряда или проблем, связанных с влажностью. | |
Выбор и обслуживание оборудования | -Выбор оборудования: Высокопроизводительные машины для очистки и сушки повышают эффективность обработки и позволяют точно контролировать потенциальные проблемы в процессе обработки. | Высококачественные машины обеспечивают лучшую обработку и снижают вероятность ошибок при очистке и сушке. |
-Техническое обслуживание оборудования: Регулярный осмотр и техническое обслуживание оборудования обеспечивают его оптимальное рабочее состояние, гарантируя качество щепы. | Правильное техническое обслуживание предотвращает выход оборудования из строя, обеспечивая надежную и качественную обработку. |
Очистка и сушка после резки
Этапы очистки и сушки после резки пластин являются сложными и деликатными процессами, требующими тщательного рассмотрения множества факторов для обеспечения конечного результата обработки. Используя научные методы и строгие процедуры, можно гарантировать, что каждый чип поступит на последующие этапы упаковки и тестирования в оптимальном состоянии.
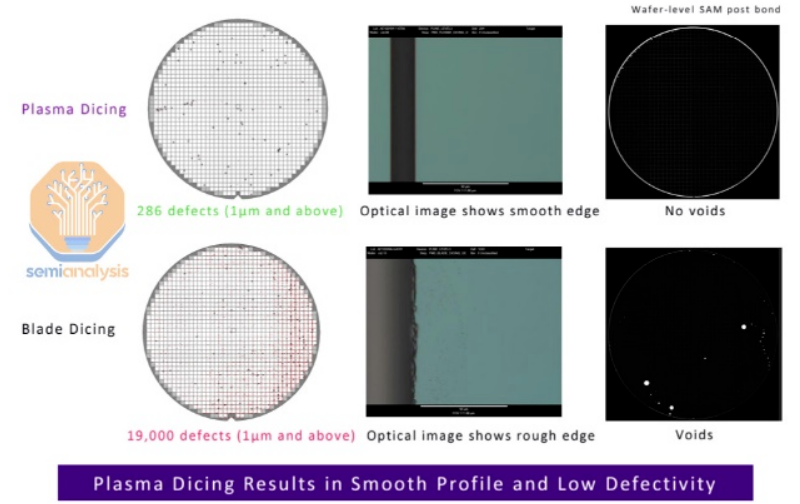
Проверка и тестирование после резки
Шаг | Содержание | Влияние |
Этап проверки | 1.Визуальный осмотр: Используйте визуальное или автоматизированное инспекционное оборудование для проверки видимых дефектов, таких как трещины, сколы или загрязнения на поверхности чипа. Быстро определяйте физически поврежденные чипы, чтобы избежать отходов. | Помогает выявлять и устранять дефектные стружки на ранних этапах процесса, сокращая потери материала. |
2.Размер Измерение: Используйте прецизионные измерительные приборы для точного измерения размеров чипа, гарантируя соответствие размера реза проектным спецификациям и предотвращая проблемы с производительностью или сложности с упаковкой. | Гарантирует, что чипы соответствуют требуемым размерам, предотвращая снижение производительности или проблемы со сборкой. | |
3.Испытание электрических характеристик: Оценка ключевых электрических параметров, таких как сопротивление, емкость и индуктивность, для выявления несоответствующих чипов и обеспечения перехода на следующий этап только чипов, соответствующих требованиям. | Гарантирует, что в процесс поступают только функциональные и проверенные на производительность чипы, что снижает риск сбоев на более поздних этапах. | |
Тестовый шаг | 1.Функциональное тестирование: Проверка того, что основные функции чипа работают должным образом, выявление и устранение чипов с функциональными отклонениями. | Обеспечивает соответствие чипов основным эксплуатационным требованиям перед передачей на последующие этапы. |
2.Тестирование надежности: Оценка стабильности работы микросхемы при длительном использовании или в суровых условиях, обычно включающих высокотемпературное старение, низкотемпературные испытания и испытания на влажность для имитации реальных экстремальных условий. | Гарантирует надежную работу чипов в различных условиях окружающей среды, повышая долговечность и стабильность продукта. | |
3.Тестирование совместимости: Убедитесь, что микросхема правильно работает с другими компонентами или системами, гарантируя отсутствие сбоев или ухудшения производительности из-за несовместимости. | Обеспечивает бесперебойную работу в реальных приложениях, предотвращая проблемы совместимости. |
3.3 Упаковка и хранение
После резки пластин чипы являются важнейшим продуктом процесса производства полупроводников, и этапы их упаковки и хранения не менее важны. Правильные меры упаковки и хранения важны не только для обеспечения безопасности и стабильности чипов во время транспортировки и хранения, но и для обеспечения надежной поддержки последующих этапов производства, тестирования и упаковки.
Краткое описание этапов проверки и тестирования:
Этапы проверки и тестирования чипов после резки пластин охватывают ряд аспектов, включая визуальный осмотр, измерение размеров, тестирование электрических характеристик, функциональное тестирование, тестирование надежности и тестирование совместимости. Эти этапы взаимосвязаны и дополняют друг друга, образуя прочный барьер для обеспечения качества и надежности продукта. Благодаря строгим процедурам проверки и тестирования потенциальные проблемы могут быть выявлены и оперативно устранены, что гарантирует соответствие конечного продукта требованиям и ожиданиям клиентов.
Аспект | Содержание |
Меры по упаковке | 1.Антистатический: Упаковочные материалы должны обладать отличными антистатическими свойствами, чтобы предотвратить повреждение устройств статическим электричеством или ухудшение их характеристик. |
2.Влагостойкий: Упаковочные материалы должны обладать хорошей влагостойкостью, чтобы предотвратить коррозию и ухудшение электрических характеристик, вызванные влажностью. | |
3.Ударопрочный: Упаковочные материалы должны обеспечивать эффективную амортизацию, чтобы защитить чипсы от вибрации и ударов во время транспортировки. | |
Среда хранения | 1.Контроль влажности: Строго контролируйте влажность в пределах соответствующего диапазона, чтобы предотвратить впитывание влаги и коррозию, вызванные чрезмерной влажностью, или проблемы со статическим электричеством, вызванные низкой влажностью. |
2.Чистота: Поддерживайте чистоту в месте хранения, чтобы избежать загрязнения щепы пылью и примесями. | |
3.Контроль температуры: Установите разумный температурный диапазон и поддерживайте стабильность температуры, чтобы предотвратить ускоренное старение из-за чрезмерного нагрева или проблем с конденсацией, вызванных низкими температурами. | |
Регулярный осмотр | Регулярно проверяйте и оценивайте хранящиеся чипы, используя визуальные осмотры, измерения размеров и тесты электрических характеристик, чтобы своевременно выявлять и устранять потенциальные проблемы. Исходя из времени и условий хранения, планируйте использование чипов, чтобы гарантировать их использование в оптимальном состоянии. |
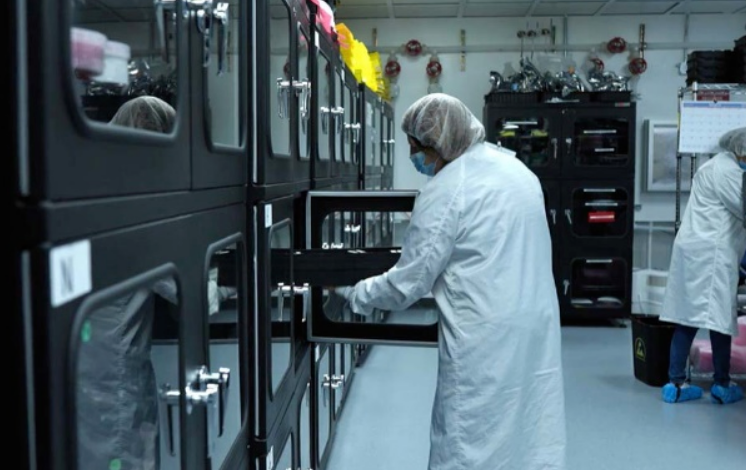
Проблема микротрещин и повреждений в процессе резки пластин является существенной проблемой в производстве полупроводников. Напряжение резки является основной причиной этого явления, поскольку оно создает крошечные трещины и повреждения на поверхности пластины, что приводит к увеличению производственных затрат и снижению качества продукции.
Чтобы решить эту проблему, крайне важно минимизировать напряжение резки и внедрить оптимизированные методы резки, инструменты и условия. Тщательное внимание к таким факторам, как материал лезвия, скорость резки, давление и методы охлаждения, может помочь уменьшить образование микротрещин и улучшить общую производительность процесса. Кроме того, продолжающиеся исследования более передовых технологий резки, таких как лазерная резка, изучают способы дальнейшего смягчения этих проблем.
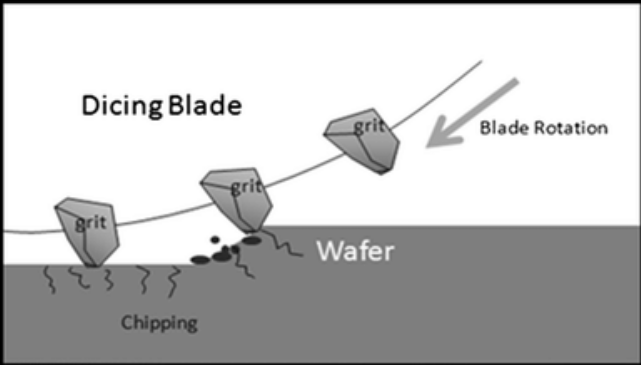
Как хрупкий материал, пластины подвержены внутренним структурным изменениям при воздействии механического, термического или химического напряжения, что приводит к образованию микротрещин. Хотя эти трещины могут быть не сразу заметны, они могут расширяться и вызывать более серьезные повреждения по мере продвижения процесса производства. Эта проблема становится особенно проблематичной на последующих этапах упаковки и тестирования, где колебания температуры и дополнительные механические напряжения могут привести к тому, что эти микротрещины превратятся в видимые изломы, что может привести к выходу чипа из строя.
Чтобы снизить этот риск, необходимо тщательно контролировать процесс резки, оптимизируя такие параметры, как скорость резки, давление и температура. Использование менее агрессивных методов резки, таких как лазерная нарезка, может снизить механическое напряжение на пластине и минимизировать образование микротрещин. Кроме того, внедрение передовых методов контроля, таких как инфракрасное сканирование или рентгеновское сканирование во время процесса нарезки пластин, может помочь обнаружить эти ранние трещины, прежде чем они вызовут дальнейшие повреждения.
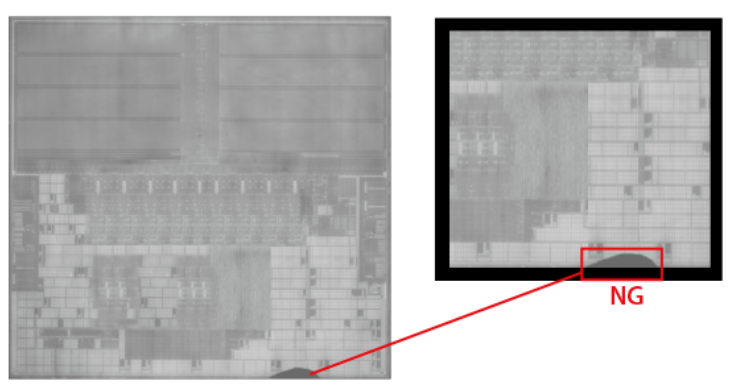
Повреждение поверхности пластины является серьезной проблемой в процессе резки, поскольку оно может напрямую повлиять на производительность и надежность чипа. Такие повреждения могут быть вызваны неправильным использованием режущих инструментов, неправильными параметрами резки или дефектами материала, присущими самой пластине. Независимо от причины, эти повреждения могут привести к изменениям электрического сопротивления или емкости схемы, что повлияет на общую производительность.
Для решения этих проблем изучаются две ключевые стратегии:
1.Оптимизация режущего инструмента и параметров: Используя более острые лезвия, регулируя скорость резки и изменяя глубину резки, можно свести к минимуму концентрацию напряжений в процессе резки, тем самым уменьшая вероятность повреждения.
2.Изучение новых технологий резки: Продвинутые технологии, такие как лазерная и плазменная резка, обеспечивают повышенную точность, потенциально снижая уровень повреждений, наносимых пластине. Эти технологии изучаются, чтобы найти способы достижения высокой точности резки, минимизируя при этом термическую и механическую нагрузку на пластину.
Зона термического воздействия и ее влияние на производительность
В процессах термической резки, таких как лазерная и плазменная резка, высокие температуры неизбежно создают зону термического воздействия на поверхности пластины. Эта область, где градиент температуры значителен, может изменить свойства материала, влияя на конечную производительность чипа.
Влияние зоны термического влияния (ЗТВ):
Изменения кристаллической структуры: При высоких температурах атомы в материале пластины могут перестраиваться, вызывая искажения в кристаллической структуре. Это искажение ослабляет материал, снижая его механическую прочность и стабильность, что увеличивает риск выхода чипа из строя во время использования.
Изменения электрических свойств: Высокие температуры могут изменить концентрацию и подвижность носителей в полупроводниковых материалах, влияя на электропроводность чипа и эффективность передачи тока. Эти изменения могут привести к снижению производительности чипа, что потенциально делает его непригодным для использования по назначению.
Для смягчения этих эффектов важнейшими стратегиями являются контроль температуры во время резки, оптимизация параметров резки и изучение таких методов, как охлаждающие струи или последующая обработка, которые позволяют снизить степень термического воздействия и сохранить целостность материала.
В целом, как микротрещины, так и зоны термического воздействия являются критическими проблемами в технологии резки пластин. Для улучшения качества полупроводниковых продуктов и повышения их конкурентоспособности на рынке потребуются непрерывные исследования, а также технологические достижения и меры контроля качества.
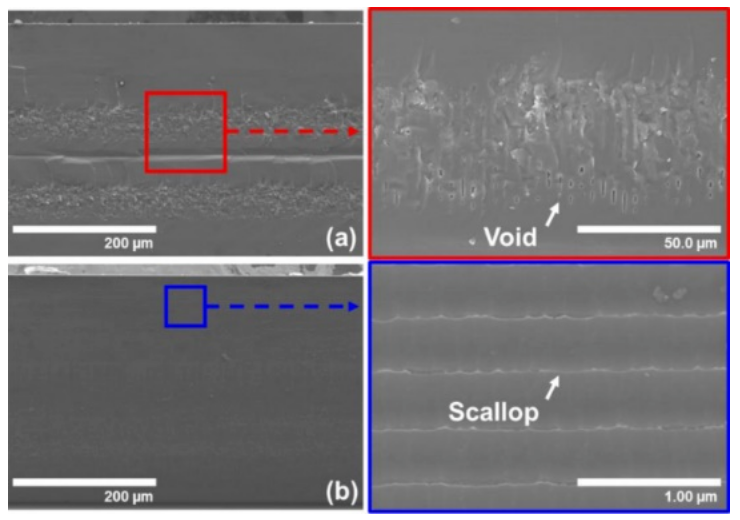
Меры по контролю зоны термического воздействия:
Оптимизация параметров процесса резки: Снижение скорости и мощности резки может эффективно минимизировать размер зоны термического воздействия (TAZ). Это помогает контролировать количество тепла, выделяемого в процессе резки, которое напрямую влияет на свойства материала пластины.
Передовые технологии охлаждения: Применение таких технологий, как охлаждение жидким азотом и микрофлюидное охлаждение, может значительно ограничить диапазон зоны термического воздействия. Эти методы охлаждения помогают рассеивать тепло более эффективно, тем самым сохраняя свойства материала пластины и минимизируя термические повреждения.
Выбор материала: Исследователи изучают новые материалы, такие как углеродные нанотрубки и графен, которые обладают превосходной теплопроводностью и механической прочностью. Эти материалы могут уменьшить зону термического воздействия, одновременно улучшая общую производительность чипов.
Подводя итог, можно сказать, что хотя зона термического воздействия является неизбежным следствием технологий термической резки, ее можно эффективно контролировать с помощью оптимизированных методов обработки и выбора материалов. Дальнейшие исследования, скорее всего, будут сосредоточены на тонкой настройке и автоматизации процессов термической резки для достижения более эффективной и точной резки пластин.

Стратегия баланса:
Достижение оптимального баланса между выходом пластин и эффективностью производства является постоянной проблемой в технологии резки пластин. Производителям необходимо учитывать множество факторов, таких как рыночный спрос, производственные затраты и качество продукции, чтобы разработать рациональную стратегию производства и параметры процесса. В то же время внедрение передового режущего оборудования, повышение квалификации операторов и усиление контроля качества сырья имеют важное значение для поддержания или даже улучшения выхода при повышении эффективности производства.
Будущие вызовы и возможности:
С развитием полупроводниковых технологий резка пластин сталкивается с новыми вызовами и возможностями. По мере уменьшения размеров чипов и увеличения интеграции требования к точности и качеству резки значительно возрастают. Одновременно с этим новые технологии предоставляют новые идеи для разработки методов резки пластин. Производители должны оставаться в курсе динамики рынка и технологических тенденций, постоянно корректируя и оптимизируя производственные стратегии и параметры процесса для удовлетворения изменений рынка и технологических требований.
В заключение следует отметить, что, учитывая рыночный спрос, производственные затраты и качество продукции, а также внедряя современное оборудование и технологии, повышая квалификацию операторов и ужесточая контроль за сырьем, производители могут достичь наилучшего баланса между выходом пластин и эффективностью производства во время резки пластин, что приведет к эффективному и высококачественному производству полупроводниковой продукции.
Перспективы на будущее:
С быстрым технологическим прогрессом полупроводниковая технология развивается беспрецедентными темпами. Как критический шаг в производстве полупроводников, технология резки пластин готова к новым захватывающим разработкам. Заглядывая вперед, ожидается, что технология резки пластин достигнет значительных улучшений в точности, эффективности и стоимости, привнося новую жизненную силу в непрерывный рост полупроводниковой промышленности.
Повышение точности:
В погоне за более высокой точностью технология резки пластин будет постоянно расширять границы существующих процессов. Глубокое изучение физических и химических механизмов процесса резки и точный контроль параметров резки позволят достичь более точных результатов резки, удовлетворяющих все более сложным требованиям к проектированию схем. Кроме того, исследование новых материалов и методов резки значительно повысит выход и качество.
Повышение эффективности:
Новое оборудование для резки пластин будет ориентировано на интеллектуальный и автоматизированный дизайн. Внедрение передовых систем управления и алгоритмов позволит оборудованию автоматически регулировать параметры резки для соответствия различным материалам и требованиям дизайна, тем самым значительно повышая эффективность производства. Такие инновации, как технология многопластинчатой резки и системы быстрой замены лезвий, будут играть решающую роль в повышении эффективности.
Сокращение затрат:
Сокращение затрат является ключевым направлением развития технологии резки пластин. По мере разработки новых материалов и методов резки ожидается, что затраты на оборудование и расходы на техническое обслуживание будут эффективно контролироваться. Кроме того, оптимизация производственных процессов и снижение уровня брака еще больше сократят отходы в процессе производства, что приведет к снижению общих производственных затрат.
Умное производство и Интернет вещей:
Интеграция интеллектуального производства и технологий Интернета вещей (IoT) привнесет преобразующие изменения в технологию резки пластин. Благодаря взаимосвязи и обмену данными между устройствами каждый шаг производственного процесса может контролироваться и оптимизироваться в режиме реального времени. Это не только повышает эффективность производства и качество продукции, но и предоставляет компаниям более точное прогнозирование рынка и поддержку в принятии решений.
В будущем технология резки пластин достигнет значительных успехов в точности, эффективности и стоимости. Эти достижения будут способствовать дальнейшему развитию полупроводниковой промышленности и принесут больше технологических инноваций и удобств человеческому обществу.
Время публикации: 19 ноября 2024 г.