Введение в карбид кремния
Карбид кремния (SiC) — это сложный полупроводниковый материал, состоящий из углерода и кремния, который является одним из идеальных материалов для изготовления высокотемпературных, высокочастотных, мощных и высоковольтных устройств. По сравнению с традиционным кремниевым материалом (Si) ширина запрещенной зоны карбида кремния в 3 раза больше, чем у кремния. Теплопроводность в 4-5 раз больше, чем у кремния; Напряжение пробоя в 8-10 раз больше, чем у кремния; Скорость электронного насыщения в 2-3 раза больше, чем у кремния, что соответствует потребностям современной промышленности в высокой мощности, высоком напряжении и высокой частоте. Он в основном используется для производства высокоскоростных, высокочастотных, мощных и светоизлучающих электронных компонентов. К областям последующего применения относятся интеллектуальные сети, новые энергетические транспортные средства, фотоэлектрическая ветроэнергетика, связь 5G и т. д. Диоды и МОП-транзисторы из карбида кремния нашли коммерческое применение.
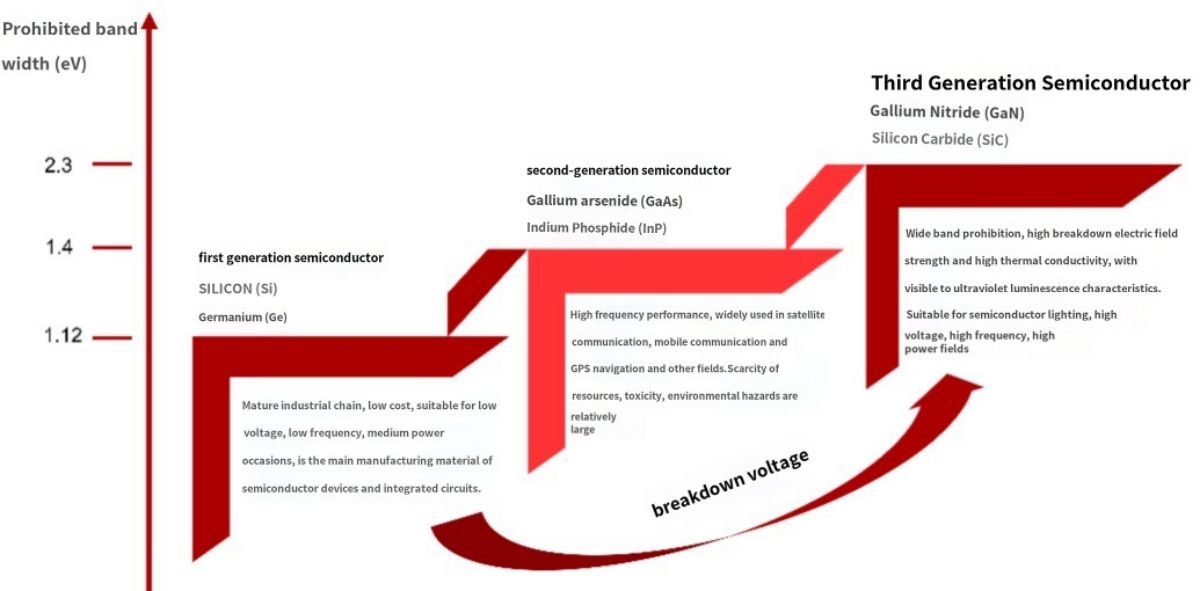
Высокая термостойкость. Ширина запрещённой зоны карбида кремния в 2-3 раза больше, чем у кремния. Электроны нелегко перемещаются при высоких температурах и могут выдерживать более высокие рабочие температуры. Теплопроводность карбида кремния в 4-5 раз выше, чем у кремния, что облегчает рассеивание тепла и повышает предельную рабочую температуру. Высокая термостойкость позволяет значительно увеличить плотность мощности, одновременно снижая требования к системе охлаждения, что делает терминал легче и компактнее.
Выдерживает высокое давление. Пробивная электрическое поле карбида кремния в 10 раз выше, чем у кремния, что позволяет ему выдерживать более высокие напряжения и лучше подходит для высоковольтных устройств.
Высокочастотное сопротивление. Карбид кремния имеет скорость дрейфа электронов при насыщении, вдвое превышающую скорость дрейфа кремния, что обеспечивает отсутствие «шлейфа» тока в процессе отключения, что позволяет эффективно повысить частоту переключения устройства и добиться его миниатюризации.
Низкие потери энергии. По сравнению с кремнием, карбид кремния обладает очень низким сопротивлением и малыми потерями во включенном состоянии. В то же время, большая ширина запрещённой зоны карбида кремния значительно снижает ток утечки и потери мощности. Кроме того, в карбидкремниевых приборах отсутствует эффект «заноса» тока в процессе выключения, а коммутационные потери низки.
Цепочка предприятий по производству карбида кремния
Он в основном включает в себя подложку, эпитаксию, проектирование устройства, производство, герметизацию и так далее. Карбид кремния от материала до полупроводникового силового прибора будет проходить через рост монокристалла, нарезку слитка, эпитаксиальный рост, проектирование пластины, производство, упаковку и другие процессы. После синтеза порошка карбида кремния сначала изготавливается слиток карбида кремния, затем путем нарезки, шлифовки и полировки получается подложка карбида кремния, а эпитаксиальным ростом получается эпитаксиальный лист. Эпитаксиальная пластина изготавливается из карбида кремния с помощью литографии, травления, ионной имплантации, пассивации металла и других процессов, пластина разрезается на кристаллы, устройство упаковывается, и устройство объединяется в специальную оболочку и собирается в модуль.
Восходящая часть производственной цепочки 1: подложка - выращивание кристалла является основным звеном процесса
На подложку из карбида кремния приходится около 47% стоимости устройств из карбида кремния, самые высокие технические барьеры при производстве, наибольшая стоимость, это ядро будущей крупномасштабной индустриализации SiC.
С точки зрения различий в электрохимических свойствах материалы подложки из карбида кремния можно разделить на проводящие подложки (область удельного сопротивления 15 ~ 30 мОм · см) и полуизолированные подложки (сопротивление выше 105 Ом · см). Эти два вида подложек используются для изготовления дискретных устройств, таких как силовые приборы и радиочастотные устройства соответственно после эпитаксиального роста. Среди них полуизолированная подложка из карбида кремния в основном используется в производстве СВЧ-устройств на основе нитрида галлия, фотоэлектрических устройств и так далее. Выращивая эпитаксиальный слой gan на полуизолированной подложке SIC, получают эпитаксиальную пластину sic, из которой в дальнейшем можно изготовить изонитридные СВЧ-устройства HEMT gan. Проводящая подложка из карбида кремния в основном используется в производстве силовых устройств. В отличие от традиционного процесса производства кремниевых силовых устройств, силовое устройство на основе карбида кремния невозможно изготовить непосредственно на подложке из карбида кремния, эпитаксиальный слой карбида кремния необходимо вырастить на проводящей подложке, чтобы получить эпитаксиальный лист карбида кремния, а эпитаксиальный слой изготавливается на диодах Шоттки, МОП-транзисторах, БТИЗ и других силовых устройствах.
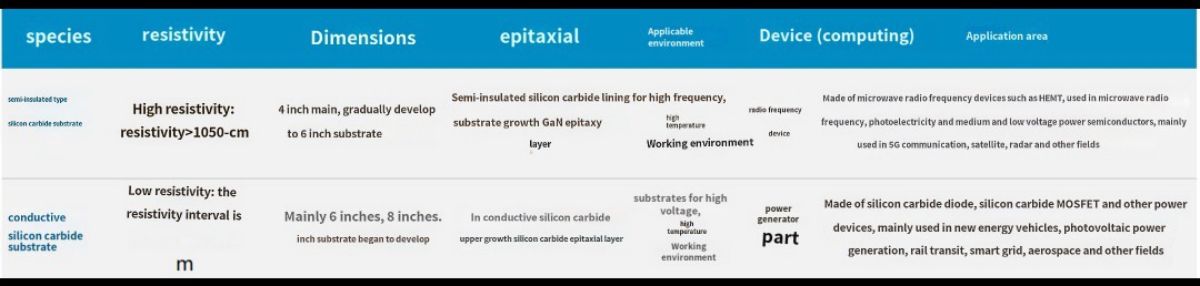
Порошок карбида кремния был синтезирован из порошка углерода высокой чистоты и порошка кремния высокой чистоты, после чего в специальном температурном поле были выращены слитки карбида кремния различных размеров, после чего с помощью нескольких технологических процессов была изготовлена подложка из карбида кремния. Основной процесс включает в себя:
Синтез сырья: порошок кремния высокой чистоты и тонер смешиваются в соответствии с формулой, и реакция проводится в реакционной камере при температуре выше 2000°C для синтеза частиц карбида кремния с определенным типом кристаллов и размером частиц. Затем, посредством дробления, просеивания, очистки и других процессов, достигается соответствие требованиям к исходному сырью из порошка карбида кремния высокой чистоты.
Выращивание кристаллов является основным процессом производства подложек из карбида кремния, определяющим их электрические свойства. В настоящее время основными методами выращивания кристаллов являются физический перенос из паровой фазы (PVT), высокотемпературное химическое осаждение из паровой фазы (HT-CVD) и жидкофазная эпитаксия (LPE). Среди них метод PVT является основным методом промышленного выращивания подложек из SiC, обладающим наибольшей технической зрелостью и наиболее широко применяемым в технике.
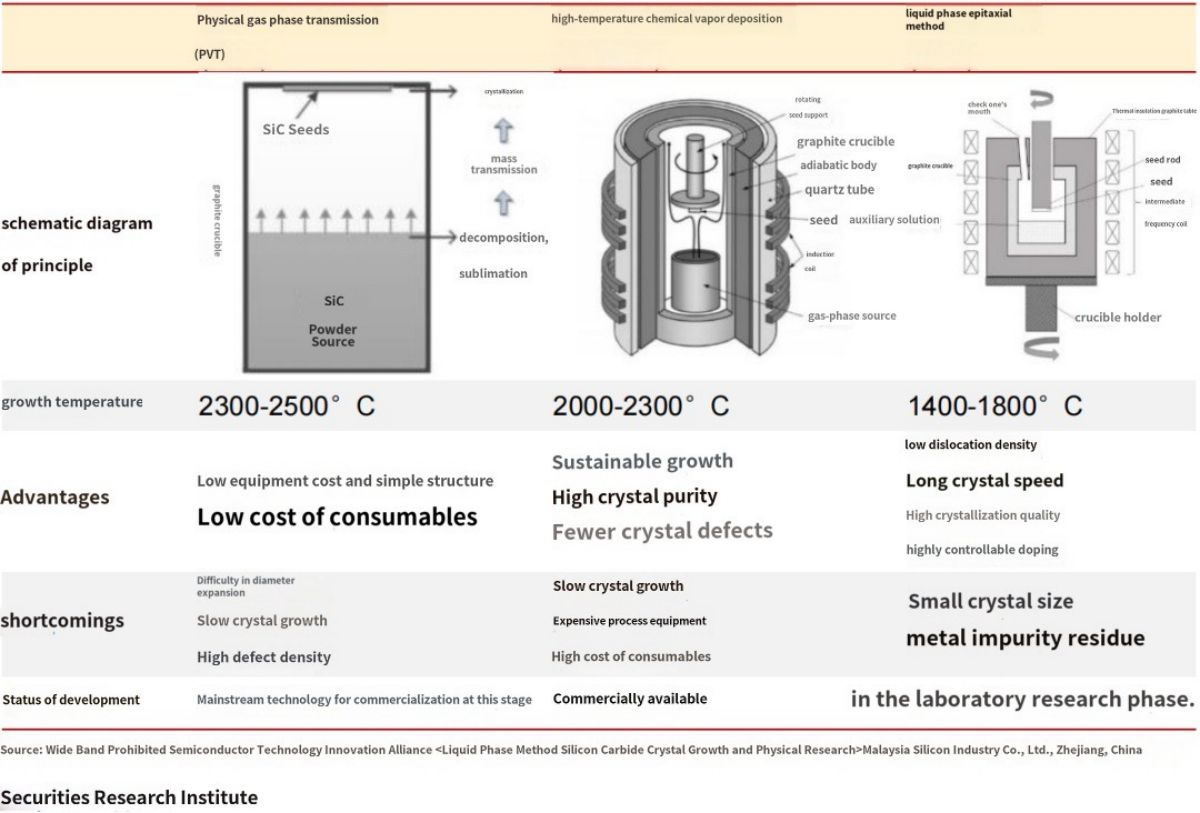
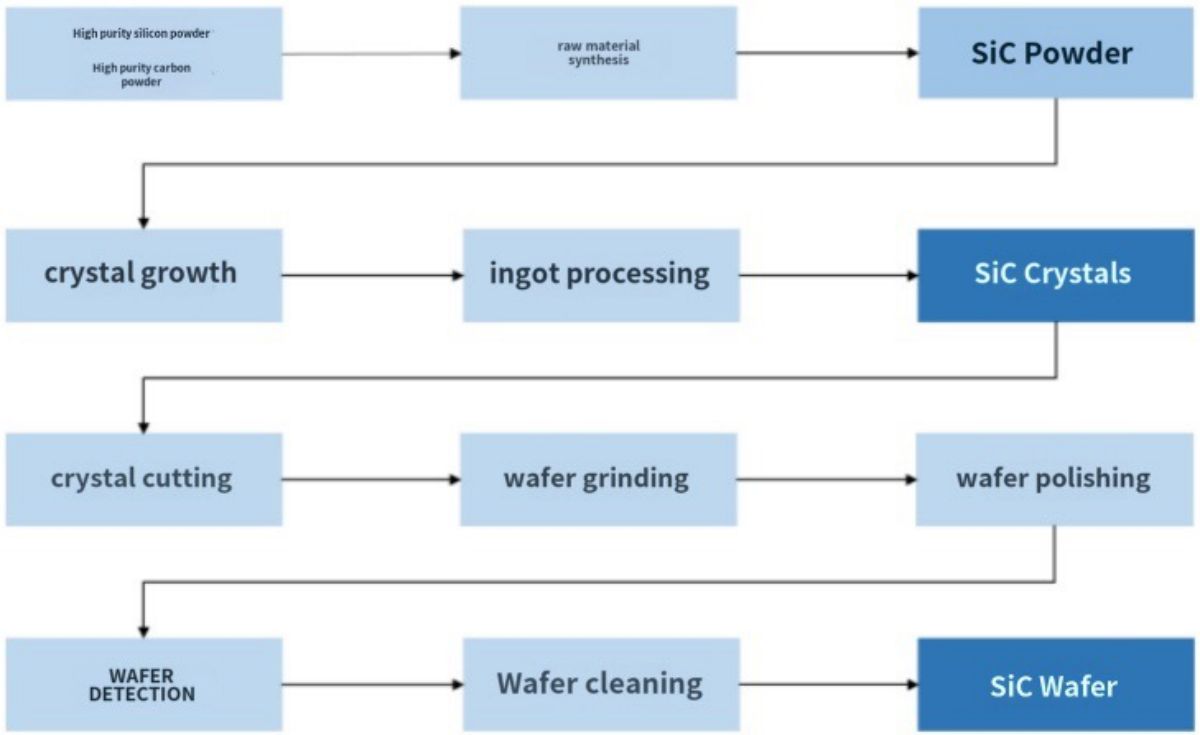
Подготовка подложки SiC сложна, что приводит к ее высокой стоимости.
Управление температурным полем затруднено: для роста стержня кристалла Si требуется всего 1500 ℃, в то время как стержень кристалла SiC необходимо выращивать при высокой температуре выше 2000 ℃, и существует более 250 изомеров SiC, но основная структура монокристалла 4H-SiC для производства силовых приборов, если не осуществлять точный контроль, получит другие кристаллические структуры. Кроме того, градиент температуры в тигле определяет скорость переноса сублимации SiC, а также расположение и режим роста газообразных атомов на границе раздела кристалла, что влияет на скорость роста кристалла и качество кристалла, поэтому необходимо сформировать систематическую технологию управления температурным полем. По сравнению с материалами Si, разница в производстве SiC также заключается в высокотемпературных процессах, таких как высокотемпературная ионная имплантация, высокотемпературное окисление, высокотемпературная активация и процесс жесткой маски, требуемый этими высокотемпературными процессами.
Медленный рост кристаллов: скорость роста стержня кристалла Si может достигать 30 ~ 150 мм/ч, а производство стержня кристалла кремния размером 1-3 м занимает всего около 1 дня; например, скорость роста стержня кристалла SiC с использованием метода PVT составляет около 0,2-0,4 мм/ч, 7 дней требуется для выращивания менее 3-6 см, скорость роста составляет менее 1% кремниевого материала, производственные мощности крайне ограничены.
Высокие параметры продукта и низкий выход годных: к основным параметрам подложки SiC относятся плотность микротрубочек, плотность дислокаций, удельное сопротивление, коробление, шероховатость поверхности и т. д. Это сложная системная инженерия, позволяющая расположить атомы в закрытой высокотемпературной камере и завершить рост кристалла, контролируя при этом индексы параметров.
Материал отличается высокой твёрдостью, высокой хрупкостью, длительным временем резания и высоким износом: твёрдость SiC по шкале Мооса составляет 9,25, что уступает только алмазу, что значительно усложняет резку, шлифовку и полировку. Для резки 35–40 деталей из слитка толщиной 3 см требуется около 120 часов. Кроме того, из-за высокой хрупкости SiC износ при обработке пластин будет больше, а выход готовой продукции составит всего около 60%.
Тенденция развития: увеличение размера + снижение цены
Глобальный рынок SiC с 6-дюймовой производственной линией развивается, и ведущие компании вышли на 8-дюймовый рынок. Внутренние проекты по разработке в основном касаются 6 дюймов. В настоящее время, хотя большинство отечественных компаний по-прежнему базируются на 4-дюймовых производственных линиях, но отрасль постепенно расширяется до 6 дюймов, с развитием технологии вспомогательного оборудования для 6 дюймов внутренняя технология подложек SiC также постепенно совершенствуется, что отражает экономию масштаба крупногабаритных производственных линий, и текущий разрыв во времени массового производства 6 дюймов внутри страны сократился до 7 лет. Больший размер пластины может привести к увеличению количества отдельных кристаллов, повышению нормы выхода годных и снижению доли краевых кристаллов, а затраты на исследования и разработки и потери выхода будут поддерживаться на уровне около 7%, тем самым улучшая использование пластины.
В конструкции устройства все еще много трудностей.
Коммерциализация SiC-диодов постепенно улучшается. В настоящее время ряд китайских производителей разработали SiC SBD-диоды. SiC SBD-диоды среднего и высокого напряжения обладают хорошей стабильностью. В бортовых автомобильных транзисторах (OBC) применение SiC SBD+SI IGBT обеспечивает стабильную плотность тока. В настоящее время в Китае отсутствуют препятствия для патентования SiC SBD-диодов, и разрыв с зарубежными странами невелик.
SiC МОП-транзисторы по-прежнему сталкиваются с множеством трудностей, разрыв между SiC МОП и зарубежными производителями всё ещё существует, а соответствующая производственная платформа всё ещё находится в стадии разработки. В настоящее время компании ST, Infineon, Rohm и другие SiC МОП-транзисторы с напряжением 600–1700 В уже освоили массовое производство, подписали контракты и поставляют продукцию многим производственным компаниям. В то же время, разработка отечественных SiC МОП-транзисторов практически завершена. Ряд производителей сотрудничают с фабриками на этапе производства пластин, а для последующей проверки заказчиком требуется время, поэтому до широкомасштабного коммерциализации ещё далеко.
В настоящее время планарная структура является основным выбором, а траншейный тип в будущем будет широко использоваться в области высокого давления. Производителей SiC-МОП-транзисторов с планарной структурой много. По сравнению с канавочной структурой, планарная структура менее подвержена проблемам локального пробоя, что влияет на стабильность работы. На рынке с напряжением ниже 1200 В планарная структура имеет широкий спектр применения, а планарная структура относительно проста в изготовлении, что позволяет удовлетворить два аспекта: технологичность и контроль затрат. Канавочная структура обладает такими преимуществами, как чрезвычайно низкая паразитная индуктивность, высокая скорость переключения, низкие потери и относительно высокая производительность.
2--Новости о SiC-пластинах
Рост производства и продаж на рынке карбида кремния, обратите внимание на структурный дисбаланс между спросом и предложением
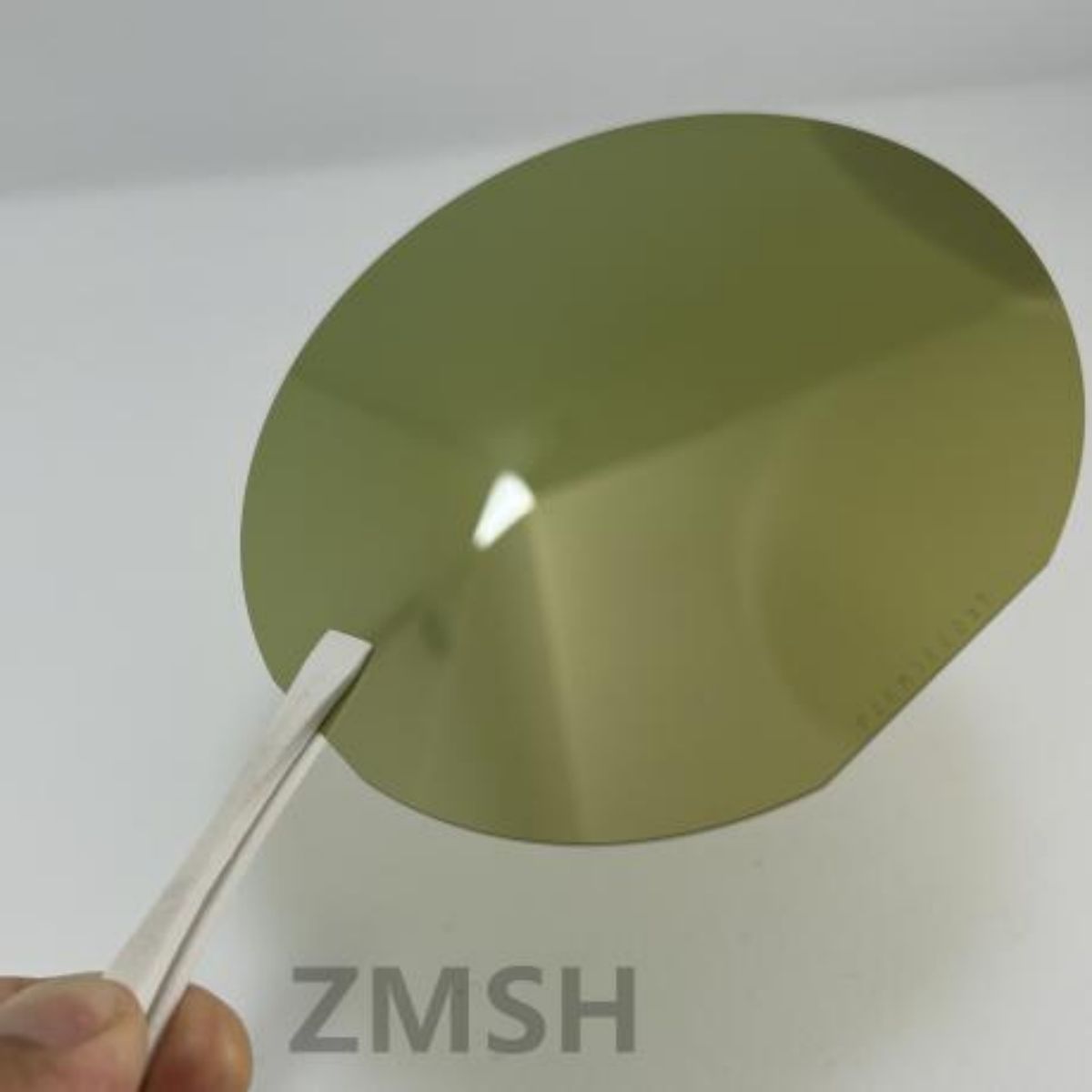
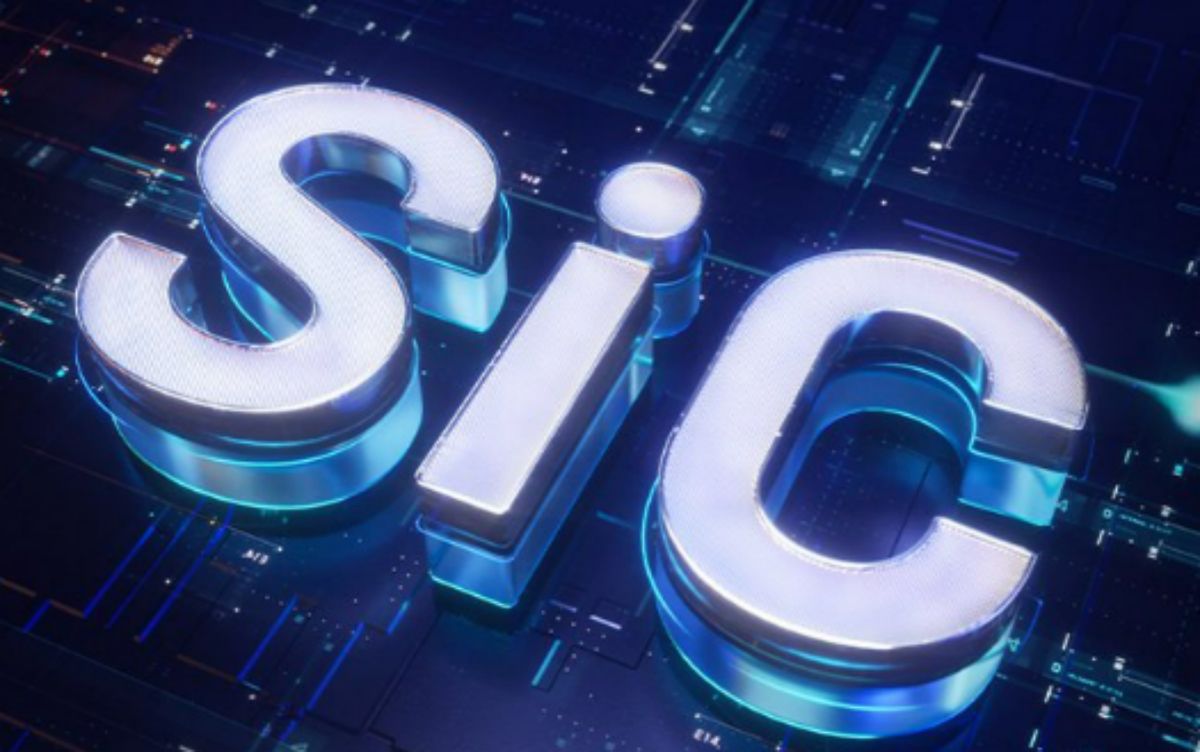
В связи с быстрым ростом спроса на высокочастотную и мощную силовую электронику, физические ограничения кремниевых полупроводниковых приборов постепенно стали очевидными, и полупроводниковые материалы третьего поколения, представленные карбидом кремния (SiC), постепенно стали промышленно осваиваться. С точки зрения эксплуатационных характеристик, карбид кремния имеет ширину запрещенной зоны в 3 раза больше, чем кремний, в 10 раз больше критической пробивной напряженности электрического поля и в 3 раза выше теплопроводность, поэтому силовые приборы на основе карбида кремния подходят для высокочастотных применений, высокого давления, высоких температур и других областей применения, способствуя повышению эффективности и удельной мощности силовых электронных систем.
В настоящее время на рынке постепенно появляются SiC-диоды и SiC MOSFET, а также более зрелые продукты, среди которых SiC-диоды широко используются вместо кремниевых диодов в некоторых областях, поскольку они не обладают преимуществом обратного восстановления заряда; SiC MOSFET также постепенно используются в автомобильной промышленности, накоплении энергии, зарядных устройствах, фотоэлектрических и других областях; в области автомобильных применений все более заметной становится тенденция к модуляризации, для достижения превосходных характеристик SiC необходимо опираться на передовые процессы упаковки, технически с относительно зрелой герметизацией корпуса в качестве основного направления, будущего или разработки пластиковых герметиков, ее индивидуальные характеристики разработки больше подходят для SiC-модулей.
Скорость падения цен на карбид кремния превосходит все ожидания
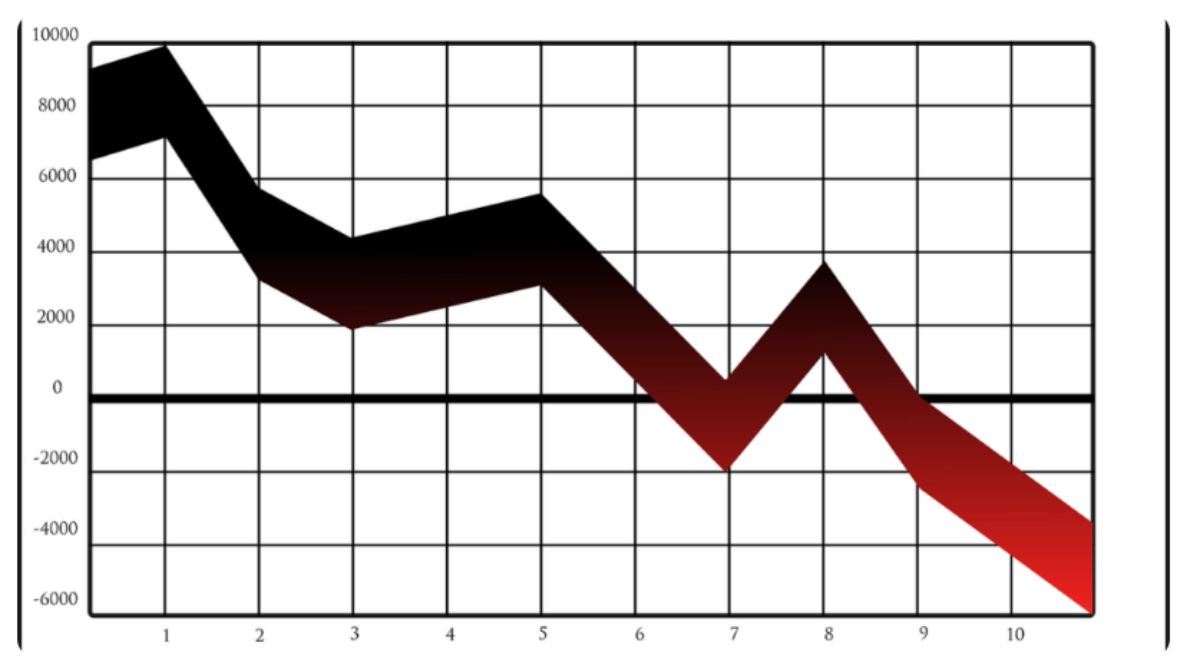
Применение устройств на основе карбида кремния ограничивается главным образом высокой стоимостью. Цена SiC MOSFET того же уровня в 4 раза выше, чем у Si IGBT. Это связано со сложностью процесса производства карбида кремния, при котором выращивание монокристаллов и эпитаксальных транзисторов не только негативно сказывается на окружающей среде, но и характеризуется низкой скоростью роста, а обработка монокристаллов в подложку требует резки и полировки. В связи с особенностями материала и неразвитостью технологии переработки, выход годных подложек отечественного производства составляет менее 50%, что обуславливает высокую стоимость подложек и эпитаксальных транзисторов.
Однако структура затрат на устройства на основе карбида кремния и устройства на основе кремния диаметрально противоположна: затраты на подложку и эпитаксию фронтального канала составляют 47% и 23% от общей стоимости устройства соответственно, что составляет около 70%, проектирование, изготовление и герметизация соединений тыльного канала составляют всего 30%, себестоимость производства кремниевых устройств в основном сосредоточена на изготовлении пластин тыльного канала (около 50%), а стоимость подложки составляет всего 7%. Феномен перевернутой цепочки стоимости в отрасли производства карбида кремния означает, что производители эпитаксии подложки, работающие на верхних звеньях цепочки, имеют основное право голоса, что является ключом к структуре отечественных и зарубежных предприятий.
С точки зрения динамики рынка, снижение стоимости карбида кремния, наряду с совершенствованием процесса получения и нарезки длинных кристаллов карбида кремния, также способствует увеличению размера пластин. Это также является проверенным путём развития полупроводников. Данные Wolfspeed показывают, что увеличение размера подложки из карбида кремния с 6 до 8 дюймов позволяет увеличить производство качественных кристаллов на 80–90% и повысить выход годных. Это позволяет снизить общую себестоимость единицы продукции на 50%.
2023 год известен как «первый год 8-дюймового SiC». В этом году отечественные и зарубежные производители карбида кремния ускоряют разработку 8-дюймового карбида кремния. Например, компания Wolfspeed вложила сумасшедшие инвестиции в размере 14,55 млрд долларов США в расширение производства карбида кремния, важной частью которого является строительство завода по производству 8-дюймовых подложек из SiC. Чтобы обеспечить будущие поставки 200-мм голого металла из SiC ряду компаний, компании Domestic Tianyue Advanced и Tianke Heda также подписали долгосрочные соглашения с Infineon на поставку 8-дюймовых подложек из карбида кремния.
Начиная с этого года, производство карбида кремния ускорится с 6 до 8 дюймов. Wolfspeed ожидает, что к 2024 году себестоимость чипа на 8-дюймовой подложке снизится более чем на 60% по сравнению со стоимостью чипа на 6-дюймовой подложке в 2022 году, что ещё больше расширит рынок приложений, свидетельствуют данные исследования Ji Bond Consulting. Текущая доля рынка 8-дюймовых продуктов составляет менее 2%, и ожидается, что к 2026 году она вырастет примерно до 15%.
На самом деле, темпы снижения цен на подложки из карбида кремния могут превзойти воображение многих людей, текущее рыночное предложение 6-дюймовых подложек составляет 4000-5000 юаней/шт., по сравнению с началом года сильно упало, ожидается, что в следующем году они упадут ниже 4000 юаней, стоит отметить, что некоторые производители, чтобы получить первый рынок, снизили цену продажи до линии себестоимости ниже, открыли модель ценовой войны, в основном сосредоточены на поставках подложек из карбида кремния, были относительно достаточны в области низкого напряжения, отечественные и зарубежные производители агрессивно расширяют производственные мощности или позволяют переизбытку подложек из карбида кремния достичь стадии раньше, чем предполагалось.
Время публикации: 19 января 2024 г.